Equipment & facility engineering
Proper functioning of equipment in a pharmaceutical process needs fit-for-purpose facilities. Equipment has to be qualified and the process must be validated.
To protect the safety of patients, pharmaceutical processes are strongly regulated: as a result, due to specific cGMP demands, equipment design and facility design for a pharmaceutical process require an approach that works from outside to in –, rather than inside to out, as is normally used for regular chemical processes – due to specific cGMP demands.
The facilities inside a pharmaceutical plant are strongly dependent on the way the equipment in the process is used. For example, using single-use equipment requires a different approach than using fixed equipment. The facility design starts with proper knowledge of the process and how the equipment functions within that process.
The facilities used, such as clean utilities (WFI, clean steam), black utilities (cooling water, compressed air, steam etc.) HVAC, cleaning units (CIP) should be aligned with the process and therefore also with the equipment. This requires a clear focus towards the client’s demands and pharmaceutical standards.
In most cases, new equipment has to be aligned with existing facilities. Mismatches often occur due to process and user requirements or due to the status of the facilities (for example restrictions related to capacity, clean utilities or layout)
What we offer
Adryan’s approach is to provide a proper basis of design by initiating engineering documents (URS, equipment specifications, layout studies, etc.) in order to meet clients’ expectations of obtaining properly functioning equipment that fits into the process and is integrated into the existing or adjusted facility.
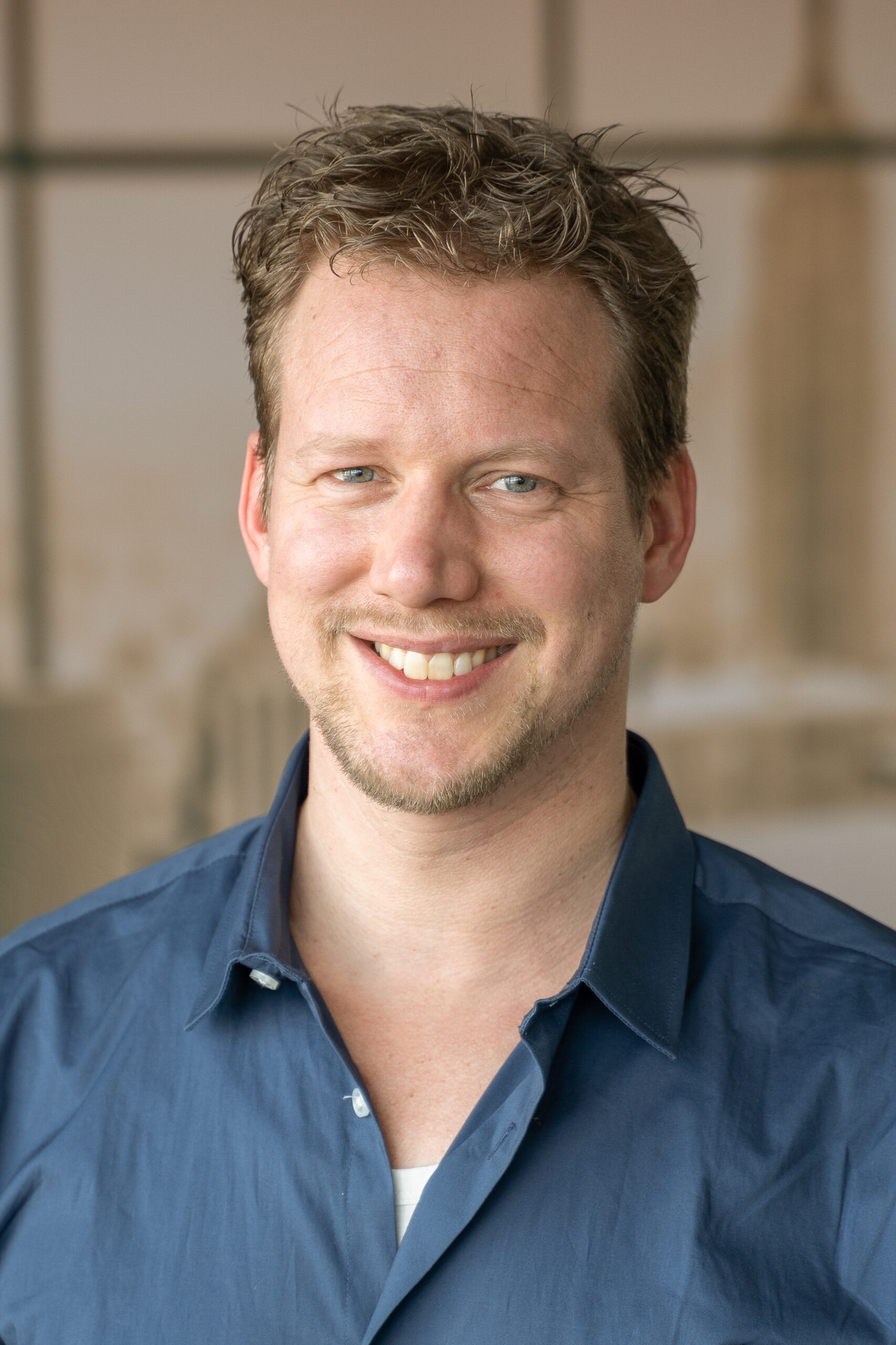
Do you want to know more about
Equipment & facility engineers